Revolutionising deburring with advanced robotics
2 mins to read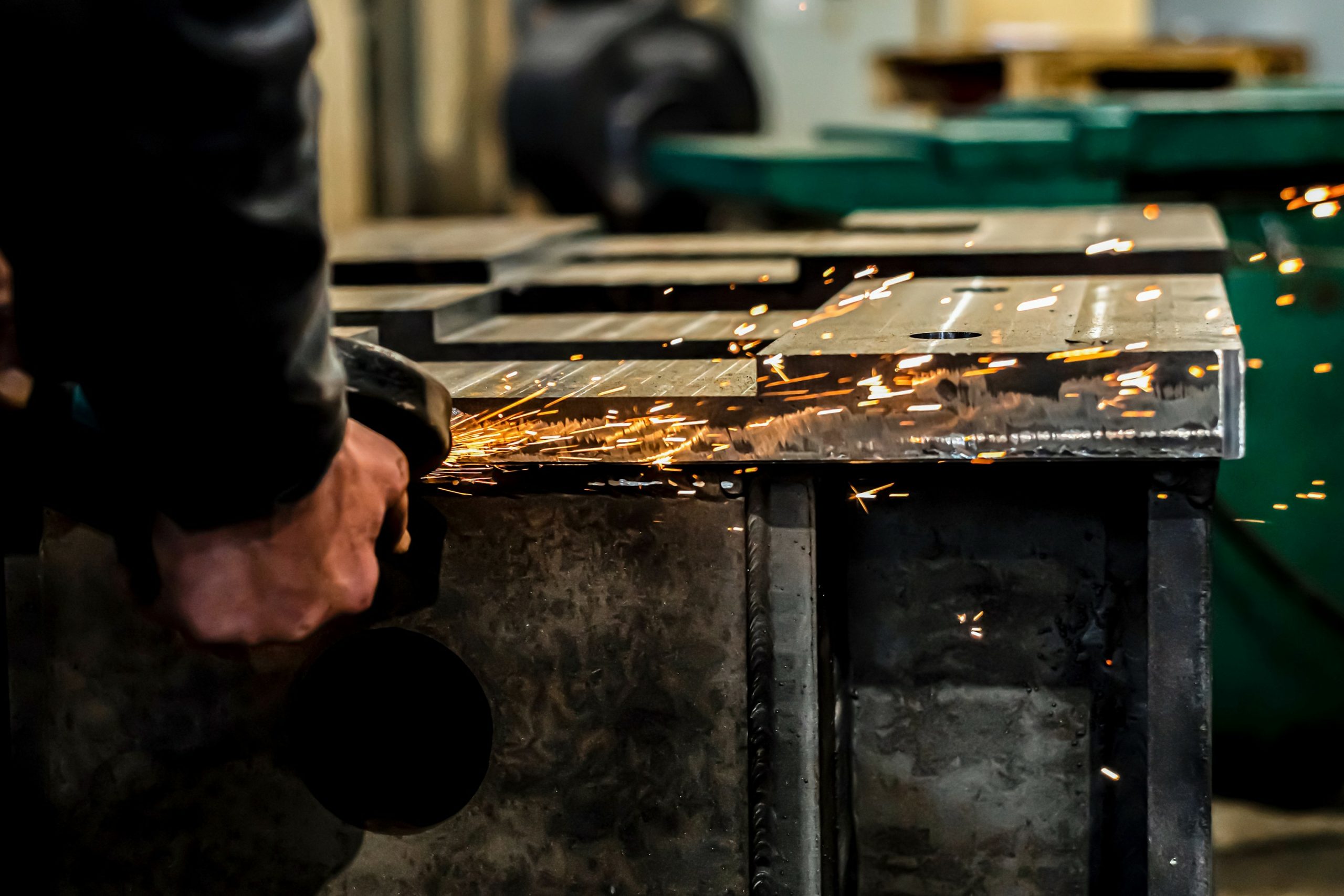
At the heart of the COGNIMAN are four concrete use cases. Sixteen project partners work on first solving these challenges and then translating the findings and solutions into toolboxes. With those, other manufacturers shall be empowered to solve their own challenges. This article focuses on the use case of GOIMEK, a precision machining company. Their large metal parts are front and centre of this use case.
In metal manufacturing, the deburring process is crucial in ensuring high-quality machined parts. Burrs, unwanted materials resulting from manufacturing, can lead to assembly or operational issues, making deburring an essential step.
Especially for large parts, deburring has been a manual effort for decades. This process is time-consuming and hard work, which is also not reproducible.
Let the robots take over!
Robotic deburring offers a promising alternative to the manual process, increasing efficiency and precision. The first step in this use case is the creation of an advanced deburring robot that can proficiently handle large metal parts while adhering to safety standards and being adaptable to varying requirements. The project sets forth the following key objectives:
- Collaborative Operation: Develop a robot capable of working harmoniously with human operators, avoiding collisions and executing simple commands.
- Cognitive Capabilities: Equip the robot with cutting-edge sensors and machine learning technology to enable autonomous deburring and quality assessment.
- Adaptive Learning: Train the robot to learn from its own experiences, enabling it to deburr parts it has not encountered before efficiently.
- Safe Autonomy: Ensure the robot can navigate the parts safely and operate autonomously without compromising safety.
Tapping into advanced technologies
By incorporating machine learning algorithms and multimodal sensors, the robot gains an in-depth understanding of the deburring task and its surroundings. Integrating a digital twin further facilitates AI training and optimisation, continuously improving the robot’s performance.
Notably, the robot will possess mapping, navigation, and guidance capabilities, enabling seamless movement during deburring operations. To validate the robot’s capabilities, the project will test it on parts from diverse sectors, including wind-power, naval and machine-tool industries, at GOIMEK’s workshop in Spain.
The deburring revolution
As far as the project partners know, there is currently no collaborative robotic technology that could be applied in the GOIMEK workshop. Too complex the tasks, too variable the movements for different parts, too difficult the integration of a robot into the shopfloor – when the COGNIMAN partners will have solved the challenge, it will represent a significant leap forward.
By developing a smart, reactive, and safe robotic solution, COGNIMAN seeks to address the limitations of traditional deburring methods while enhancing overall efficiency and quality. As this advanced deburring robot interacts seamlessly with human operators, it holds the potential to drive innovation, boost productivity and pave the way for a new era in manufacturing.
About GOIMEK
GOIMEK is a cooperative in Spain dedicated to delivering precision machining services to meet the market’s diverse needs. They have expertise in advanced machining techniques focused on producing critical components for high-demand industries such as aerospace, energy and capital equipment.
Get to know more about GOIMEK here at: https://www.goimek.com/en