Coding for autonomous deburring in precision machining
2 mins to read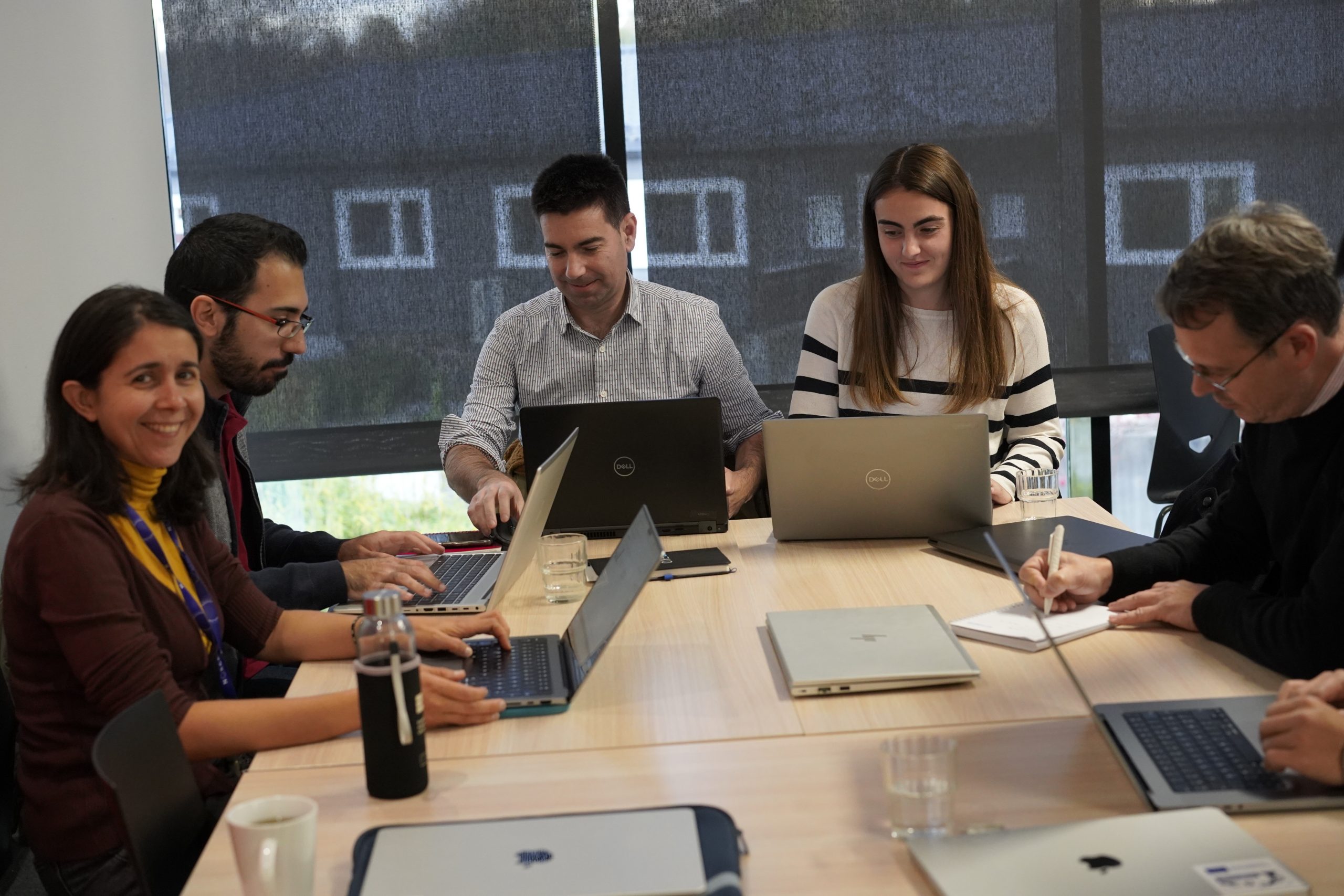
Deburring—removing excess material from parts—is a necessary but manual-labour intensive step in GOIMEK’s precision machining. The progress made during a recent COGNIMAN coding day in Kristiansand, Norway has brought automation within reach. The session brought together experts from the project partners like IBM, SINTEF, NORCE and Montimage.
Tackling deburring in large parts
At GOIMEK, the primary challenge is creating a collaborative robotic system that is both flexible and autonomous. It needs to be capable of handling diverse geometries of parts without additional instructions or operator input. A solution that reduces human intervention and increases machine adaptability would lead to significant gains in productivity while ensuring high standards of precision.
Leveraging coding and AI to solve the challenge
To create the autonomous deburring solution, COGNIMAN uses coding to introduce AI algorithms and digital twins to enable robotic arms to recognise part shapes and make decisions about the best deburring strategies. A digital twin is a virtual model of a physical object. By replicating GOIMEK’s real-world parts and processes in a digital space, the team could simulate different deburring approaches and make adjustments before applying them to actual parts.
By the end of the session, the team had made good progress in developing a prototype of the algorithm for the autonomous deburring system. This involved:
- Testing and improving the AI models responsible for part recognition
- Refining algorithms that help the system choose the right tools for deburring
- Developing solutions for real-time adaptability, ensuring the system can handle new and different parts without requiring any reprogramming
Achieving results through agile collaboration
The session benefited from a collaborative approach, with the team working together to manage code and share progress in real-time.
The coding team collaborated using GitHub, an online platform that helps people work together on coding projects. It’s like a digital workspace where everyone can store, share and update their code. GitHub also tracks every change made, making it easy to fix mistakes or revisit earlier versions of the work.
To keep track of tasks, the team used Kanban boards—a tool that organises tasks into three categories:
- To do: Tasks that need to be started
- In progress: Tasks currently being worked on
- Done: Completed tasks
Each task is represented by a digital card that moves across the board as progress is made. This simple yet powerful system helps everyone involved to see what is happening and ensures that no task gets overlooked.
What’s next?
The outcomes of this session are building blocks towards creating a truly autonomous and adaptable system for deburring. The next phases will focus on fine-tuning the integration of AI algorithms, digital twins and machine learning models to create a fully operational collaborative robotics solution that can handle the demands of deburring large precision-machined parts.